By Kelly Stacionis, Holtz Builders
Polyurethanes (PUs) are considered a miracle invention of post World War II chemistry, and are used everywhere in today’s world: adhesives, auto body parts and paints, mattresses and furniture, refrigeration panels, and the list goes on. Once cured, PUs are considered inert and non-toxic during normal conditions, but during initial install, PUs can release dangerous fumes and vapors while their chemical reactions occur. Many PUs come in two parts that get mixed together during application, but others are designed to react with the water vapor in air. Spray foam insulation and performance floor coatings are commonplace in the construction of modern buildings.
Polyurethanes contain a variety of hazardous components. Of particular concern are very reactive chemicals called isocyanates, and exposure to them is one of the leading causes of occupational asthma each year. They can also be irritating to the skin, eyes, and mucus membranes, some of them are suspected to cause cancer in humans, and even death can occur (from severe asthma attack) in workers who have been sensitized. It is estimated that 1-5% of workers with repeat exposure are sensitized.
OSHA has exposure limits on two diisocyanates, but this is a huge class of chemicals with many variations. The established exposure limits are very, very low (parts per billion!) because sensitized individuals can have severe asthmatic reactions to the tiniest exposure and can also react from skin contact alone.
It is very important that PU installers, other trade workers on the jobsite, and any occupants in the building during construction be protected. The American Chemistry Council has a special working group called the Center for the Polyurethanes Industry (CPI) that provides excellent resources for best practices and training via their website in both English and Spanish.
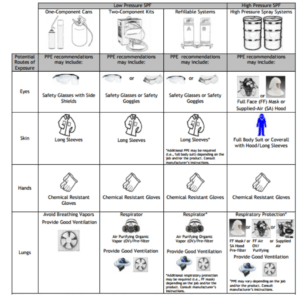
For high pressure spray systems, installers should wear a full face or supplied air respirator. All air purifying respirators need to have a prefilter in conjunction with an organic vapor cartridge, and the installer’s skin must be completely covered by appropriate, chemical resistant PPE.
Best practices based on several studies indicate PPE and engineering controls (containment zones and mechanical ventilation) should be used together during indoor installations. Guidance from CPI suggests the following depending upon work site size, layout, amount of spray foam to be installed, and manufacturer recommendations for minimum air exchange and re-entry times.
- Turn off HVAC and cover vents. Power to HVAC should be locked and tagged out.
- If needed, containment systems should fully enclose the application area with barriers that stop airflow. Negative pressure of these spaces is recommended.
- Educate other trade workers and building occupants about the hazard.
- Post clear warning signage at work zone / containment entrances with the goal of keeping other, unprotected workers out.
- Exhaust air should be directed out of the building, away from any air intakes.
- It is best practice to filter the exhaust air near the point of installation before it is released.
- Fresh, make-up air improves air turnover, reducing concentrations of hazardous PU components.
- For work sites where containment and ventilation are not feasible or required, all other unprotected workers and occupants should remain a minimum of 50 feet away from the work zone.
- Installers should work with the manufacturer to determine minimum ventilation rates, re-entry, and re-occupancy times for each unique job site. Those requirements should be shared with general contractors or homeowners in the planning phase of the project.
Figure 2: Example of a Two-Fan Ventilation System (active exhaust and supply systems) for Interior SPF Application; Ventilation Considerations for Spray Polyurethane Foam
Website references:
https://www.americanchemistry.com/industry-groups/center-for-the-polyurethanes-industry-cpi/resources-documents-library
https://www.americanchemistry.com/industry-groups/center-for-the-polyurethanes-industry-cpi/resources/library/guidance-for-selection-of-personal-protective-equipment-for-mdi-users
https://www.whysprayfoam.org/wp-content/uploads/2017/05/SPF-Ventilation-Guidance-v-3-2016.pdf
https://www.americanchemistry.com/industry-groups/center-for-the-polyurethanes-industry-cpi/resources/library/health-and-safety-product-stewardship-workbook-for-high-pressure-application-of-spray-polyurethane-foam-spf
https://www.spraypolyurethane.org/wp-content/uploads/2018/08/Info-Sheet-on-Reentry-and-Reoccupancy-Times-when-Installing-SPF-Insulation-and-Sealants.pdf